The Essential Role of a Lathe Turning Parts Factory in Modern Manufacturing
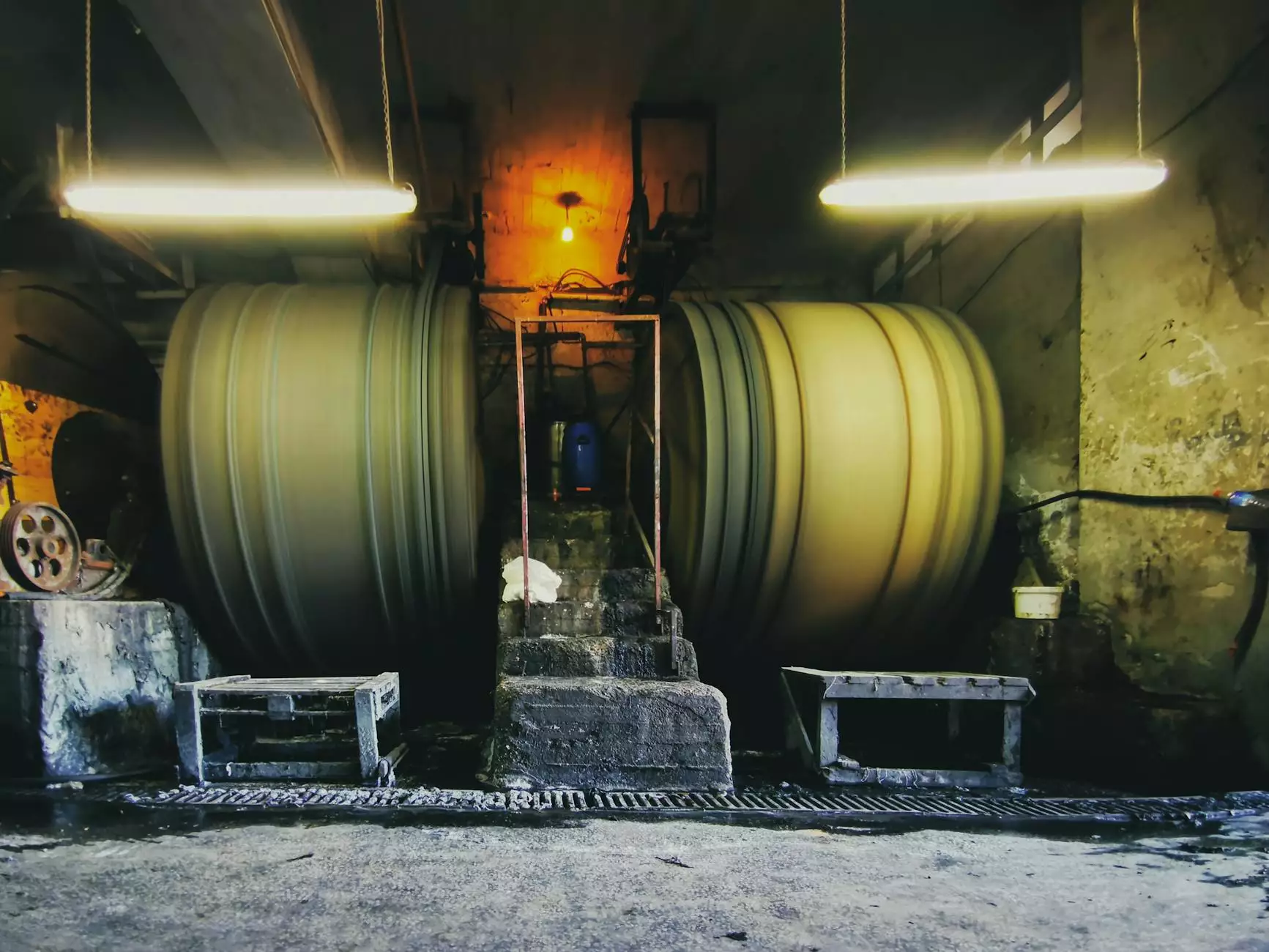
In today’s competitive landscape, the demand for high-quality parts and components is at an all-time high. Companies are consistently searching for efficient solutions that can drive productivity and ensure high standards. A lathe turning parts factory emerges as a critical player in meeting these demands. By harnessing advanced technology and skilled craftsmanship, such factories are primed to deliver precision-engineered components that serve a wide array of industries.
Understanding Lathe Turning: A Key Manufacturing Process
Lathe turning is a fundamental manufacturing process that involves the removal of material from a rotating workpiece. This method is employed to produce cylindrical shapes, grooves, and intricate designs with precision and efficiency. Utilizing various types of lathes, such as CNC lathes (computer numerical control), manufacturers can achieve unparalleled accuracy and repeatability.
The Lathe Process Explained
The process of lathe turning can be broken down into several crucial steps:
- Preparation: Selecting the appropriate material based on the application requirements.
- Setup: Ensuring that the lathe is correctly configured with the necessary tooling.
- Turning: Operating the lathe to remove material and achieve the desired shape.
- Finishing: Applying surface treatments or additional machining as needed to meet specifications.
The Benefits of Choosing a Dedicated Lathe Turning Parts Factory
When partnering with a lathe turning parts factory, companies can enjoy numerous advantages that drive efficiency and quality in production.
1. Precision Engineering
One of the most significant benefits of lathe turning is the precision it offers. High-end lathe turning equipment, especially CNC machines, can achieve tolerances as tight as 0.001 inches. This level of precision is crucial for industries such as aerospace and automotive, where even minor deviations can lead to catastrophic failures.
2. Versatility in Material Usage
Lathe turning is compatible with a wide range of materials, including:
- Metals: Aluminum, steel, titanium, and more
- Plastics: Nylon, acrylic, and other engineering plastics
- Wood: For specialized applications requiring wooden components
This versatility allows clients to find tailored solutions for their specific needs.
3. Cost-Efficiency
Utilizing a lathe turning parts factory can be a cost-effective solution. The efficiency of CNC lathes allows for high-volume production runs without sacrificing quality. Moreover, reduced cycle times and minimal waste generation lead to significant cost savings for manufacturers.
4. Customization Capabilities
Another significant advantage is the ability to create custom parts that meet unique client specifications. With the latest computer-aided design (CAD) software, it’s easy for engineers to design complex geometries and ensure they are realized during the machining process.
Applications of Lathe Turning Parts
Lathe-turned parts have a broad range of applications across various industries. Here are a few prominent sectors that benefit from this manufacturing process:
Aerospace Industry
In the aerospace industry, the demand for precision and reliability is at its peak. Lathe turning allows manufacturers to produce lightweight yet durable components essential for aircraft. Parts such as fittings, brackets, and shafts require the utmost precision, making lathe turning an indispensable process.
Automotive Sector
The automotive industry also relies heavily on lathe turning for the production of components like:
- Camshafts
- Crankshafts
- Brake rotors
- Axles
These components must meet stringent safety and performance standards, which can only be achieved through precision lathe turning.
Medical Equipment Manufacturing
With the rise of advanced medical technologies, the medical industry requires high-quality components with exact dimensions. Lathe turning plays a pivotal role in producing parts for surgical instruments, devices, and implants.
Conclusion: Choosing the Right Lathe Turning Parts Factory
The importance of selecting the right lathe turning parts factory cannot be overstated. Quality and precision should not be compromised in this critical stage of production. When looking for a partnering manufacturer, companies should prioritize:
- Experience: A proven track record in the industry.
- Technology: State-of-the-art machinery and design software.
- Quality Assurance: Robust quality control measures.
- Customer Service: Responsive and supportive communication.
By partnering with a top-tier lathe turning parts factory, businesses can enhance their production capabilities, improve product quality, and gain a competitive advantage in their respective markets. Whether you require a few custom-engineered parts or a large production run, embracing the expertise and technology of a reliable lathe turning manufacturer can transform your manufacturing processes.
Final Thoughts
The future of manufacturing is bright, thanks in part to the advancements in lathe turning technology. As industries continue to evolve, the demand for high-quality precision parts will only grow. Companies like Deep Mould, operating within the framework of metal fabricators, are well positioned to meet these needs with innovative solutions and exceptional service. Invest in quality, efficiency, and precision—choose a reputable lathe turning parts factory today.